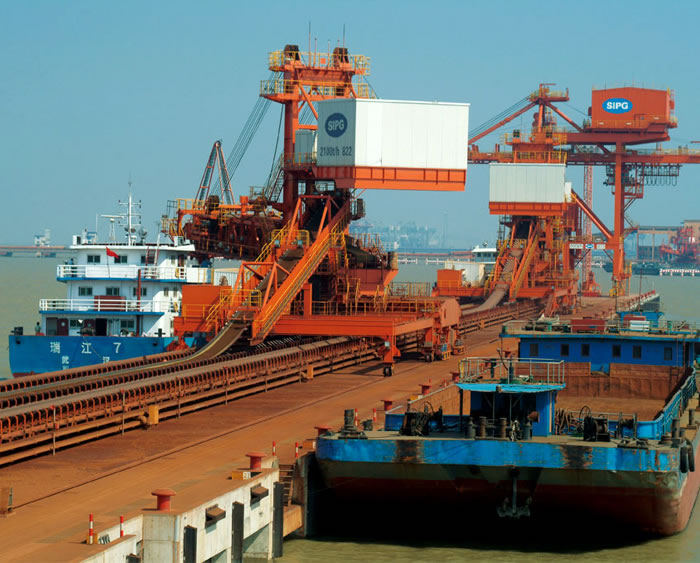
- 产品名称:电力行业解决方案
- 产品编号:EMCB1503901
- 产品概括:
- 使用精度:
一种高精度、高稳定性智能称重系统 长期使用精度±0.2%
电力行业解决方案
电厂输煤计量解决方案
发电厂精确供煤解决方案
本内容为依科电气技术中心研发并原创,拥有完全知识产权,仅在www.eaccor.com网站、依科注册的招投标平台及依科皮带秤微信公众号平台上发布,未经依科公司书面授权,请勿转载/套用,盗版必究。
火力发电厂燃煤管理现状:
煤炭作为火力发电厂高消耗型能源,直接决定着电厂的生产运营成本、能耗指标、利润空间与整体经营业绩,从入厂采样、翻卸车、堆煤、取煤、配煤,到入炉计量、给煤机分配计量,整体流程每一环节都需要环环相扣、准确到位、相互依托。近年来各集团燃料管控力度与要求更是提升至前所未有的新高度。设备部、发电部、燃料部,直至厂领导,都需要花费大量心血关注并保障相关设备安全、可靠、稳定、准确运行。燃煤入厂需要精确称重计量及准确热值分析,这是火力发电厂对外结算的总闸口。精确称重计量设备使用主要包含三个方面:1是实际运行称重计量精度;2是允差范围内精度稳定周期;3、后期维护人力、物力、财力成本控制。这是目前火力发电厂的关键痛点,也是亟待解决的核心问题,直接影响成本控制与经营业绩考核。火电厂入厂煤运输方式主要有四种:1是沿江沿河沿海船运;2是火车运输;3是汽车运输;4是坑口皮带输送。四种方式均需要对来煤数据进行复核,详细分析如下:
第1种船运传统方式是水尺结算,重大误差来源a水尺视觉差,b水温及水的密度变化,c压舱物,2%~5%的偏差是再正常不过,对于目前的大型轮船运煤,就是数十上百吨的偏差。
第2种火车运输燃料称重计量相对比较准确,但轨道衡存在维护量大、造价成本高、铁道专项经营的一系列难题和制约条件,且设备计量超差很难及时发现。
第3种汽车运输方式相对好许多,现在也有许多无人值守的汽车衡系统防止了作弊等非法操作。精度相对稳定,主要问题同样是一旦设备出现超差问题,运维人员难以及时发现,从而可能造成重大经济纠纷与损失。
第4种坑口皮带输送方式,效率高、成本低,通过皮带秤称重计量结果进行结算。以往大多数坑口电厂均为煤矿合作或自有电厂,对具体煤量的数据要求不高,所以使用普通皮带秤未暴露明显问题。但随着现代化企业经营管理要求日益严格,工业智能化、精细化理念深入人心。企业为提高核心竞争力,必须对成本进行详细、准确地核算,甚至使用工业MES系统对各个关键环节进行实时在线监控与考核。普通皮带秤暴露问题日益严重,完全不能满足实际工作需求,称重精度低、检测数据不稳定容易造成账目混乱,经常导致各部门之间推诿扯皮,严重影响企业日常经营管理工作质量与效率。
针对以上四种入厂煤计量体系的问题,如果有一种智能皮带秤可以实现高精度、自校验、免维护、高稳定性的计量,那么以上问题均迎刃而解。依科电气联合国外专家及高校导师经过数年创新研发的专利技术产品——高精度全智能矩阵皮带秤,采用目前先进的人工智能称重技术,配套特制超高灵敏度传感器及人工智能称重控制器(采用多组AD及8组以上称重单元结构,使用精度长期保持在0.2%以内,矩阵排列,校验一次稳定性周期达6个月以上,可实现无忧运行)!配置独有的智能校验系统,对每一路传感器单独AD检测,故障报警,超差剔除等功能,使皮带秤保持长期高精度、高稳定性运行。自检自校无人值守,自动校验装置安置在电子皮带秤的主秤体上,独有结构能够实时模拟输送物料的重力状态,自动完成皮带秤全过程动态校验管理,二次仪表采用SEQ-AI智能算法,矩阵控制跟踪复核技术,在运行使用状态下自动完成监控及校验修正。第1种船运可以改成高精度全智能皮带秤结算,由第三方有资质机构进行现场检定并颁发证书,保证公正结算无纠纷。第2种火车来煤,第3种汽车运输,可以通过高精度秤来实时比对,可以及时判断出极小的超差数据,防止发生重大贸易纠纷,避免损失。第4种通过将原传统皮带秤改造成高精度全智能矩阵皮带秤,可以直接实现精确核算,为各部门考核及相关结算提供坚实准确的数据。
基于国内燃料市场多样性,目前煤场燃料数字化无人值守管控是大势所趋,为有效从源头进行成本管控,各大发电集团在煤场数字化管理、多煤种深度配煤掺烧方面竞相探索创新思路、深入挖潜增效,而所有管控手段与先进技术投入生产使用的前提条件是堆煤、取煤实物称重计量的精确度。斗轮机无论是在露天煤场还是全封闭煤场堆取料,传统的斗轮机皮带秤称重方式,仅能实现上下俯仰角度的理论值补偿,导致堆、取料运行中动态称重计量的偏差很大。秤体安装于动态运行的斗轮机悬臂皮带上,且精度超差严重、稳定周期短,不具备自动自检、校验功能,每次校验只能人工到悬臂上进行手动挂码,这些因素都为后续日常维护及校验工作带来了极大的困扰,即便投入大量的人力、物力,仍不能达到预期效果。 斗轮机堆、取料运行在燃料从入厂到入炉整体动作流程中起到承上启下、运输中转的关键作用,翻卸车堆料流程效率、按煤种分区堆料储料、配煤掺烧分区取料上煤入炉等等,都需要斗轮机进行高效连续、稳定运行,根本没有多少空间、时间允许检修工作人员频繁地维护、校验悬臂皮带秤。但燃料出库、入库称重计量数据是每个发电集团必然监控的核心数据,煤场亏煤、盈煤事关重大,通过入炉煤称重数据与轨道衡称重数据进行反推来提供出库、入库称重计量数据的计算方法,引入系统误差过大且根本无从估算,且不能实时、直接、动态、高效、准确地反应实际工况,只能进行粗放式管理。综上所述,若要满足煤场精细化动态全过程管理,斗轮机皮带秤的精确度、稳定周期、实时动态计量、自动检定、自动校验、自动监控、智慧型数据辨识与处理、日常维护等方面尤为重要,可视为影响煤场整体管理水平的决定性因素。
依科电气提供的“高精度全智能斗轮机皮带秤”可以在斗轮机大车双向移动、悬臂皮带机俯仰、左右旋转等各种倾角与动作姿态动态变化的过程中进行准确称重,使用中免维护,堆、取双向独立计量精度长期保持称重准确度≤0.4%。采用8组以上矩阵称重单元,配备动态姿态重量补偿器,实时、全方位、高精度跟踪、检测移动中称重单元的立体姿态变化,实时补偿修正姿态变化对称重检测数据的扰动数值,保证皮带秤在各种工况下的稳定性与准确性。斗轮机双向堆取料称重计量皮带秤技术攻关一直是整个皮带秤计量行业的难题,更是是皮带秤行业的闪耀明珠。大唐国际盘山发电有限公司使用依科高精度全智能斗轮机皮带秤解决了困扰多年的煤场核算管理难题,并将称重数据实时上传“燃料三大项目”平台。精确的取料控制是配煤掺烧的关键环节,辅助煤场计量与深度配煤掺烧工作更加高质高效。
大唐国际盘山发电有限公司1号斗轮机
华电襄阳发电2期1号斗轮机
上一个产品:没有了
下一个产品:没有了